Comprehensive Overview: What is Porosity in Welding and Just How to stop It
Wiki Article
The Scientific Research Behind Porosity: A Comprehensive Guide for Welders and Fabricators
Recognizing the detailed systems behind porosity in welding is crucial for welders and makers pursuing remarkable workmanship. As metalworkers delve into the midsts of this sensation, they discover a world regulated by various variables that affect the development of these tiny voids within welds. From the make-up of the base products to the complexities of the welding procedure itself, a wide variety of variables conspire to either intensify or reduce the existence of porosity. In this extensive guide, we will decipher the science behind porosity, exploring its impacts on weld high quality and unveiling advanced techniques for its control. Join us on this trip via the microcosm of welding imperfections, where accuracy satisfies understanding in the quest of perfect welds.Understanding Porosity in Welding
FIRST SENTENCE:
Evaluation of porosity in welding exposes crucial understandings right into the stability and top quality of the weld joint. Porosity, defined by the existence of dental caries or voids within the weld steel, is a common worry in welding processes. These gaps, if not properly resolved, can jeopardize the architectural integrity and mechanical buildings of the weld, bring about possible failures in the ended up product.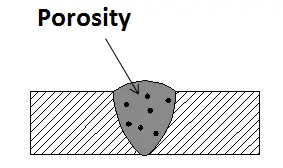
To identify and measure porosity, non-destructive screening approaches such as ultrasonic screening or X-ray examination are typically employed. These strategies enable the recognition of interior problems without endangering the stability of the weld. By analyzing the dimension, shape, and circulation of porosity within a weld, welders can make enlightened decisions to boost their welding processes and accomplish sounder weld joints.

Factors Affecting Porosity Formation
The incident of porosity in welding is influenced by a myriad of factors, ranging from gas securing efficiency to the details of welding criterion setups. One critical variable adding to porosity development is poor gas securing. When the shielding gas, commonly argon or carbon dioxide, is not efficiently covering the weld pool, atmospheric gases like oxygen and nitrogen can infect the molten metal, causing porosity. Additionally, the sanitation of the base products plays a significant role. Contaminants such as corrosion, oil, or moisture can evaporate during welding, developing gas pockets within the weld. Welding criteria, consisting of voltage, present, travel speed, and electrode type, Click Here also effect porosity formation. Making use of inappropriate settings can generate too much spatter or warm input, which subsequently can cause porosity. The welding technique used, such as gas steel arc welding (GMAW) or secured steel arc welding (SMAW), can influence porosity formation due to variants in heat circulation and gas insurance coverage. Understanding and controlling these elements are important for minimizing porosity in welding procedures.Effects of Porosity on Weld Quality
The existence of porosity likewise weakens the weld's resistance to rust, as the entraped air or gases within the voids can react with the surrounding environment, leading to degradation over time. Additionally, porosity can hinder the weld's ability to withstand stress or influence, more jeopardizing the total quality and integrity of the bonded framework. In critical applications such as aerospace, automobile, or structural constructions, where safety and security and durability are paramount, the damaging impacts of porosity on weld quality can have extreme consequences, stressing the relevance of decreasing porosity through proper welding methods and procedures.Methods to Decrease Porosity
Additionally, using the ideal welding specifications, such as the proper voltage, existing, and travel speed, is vital in preventing porosity. Keeping a constant arc length and angle throughout welding additionally assists minimize the probability of porosity.
Additionally, selecting the ideal protecting gas and preserving appropriate gas circulation prices are necessary in lessening porosity. Using the proper welding strategy, such as back-stepping or using a weaving movement, can likewise help distribute warmth evenly and minimize the possibilities of porosity formation. Finally, making certain proper air flow in the welding atmosphere to Related Site remove any potential resources of contamination is essential for accomplishing porosity-free welds. By applying these techniques, welders can efficiently decrease porosity and produce high-quality bonded joints.
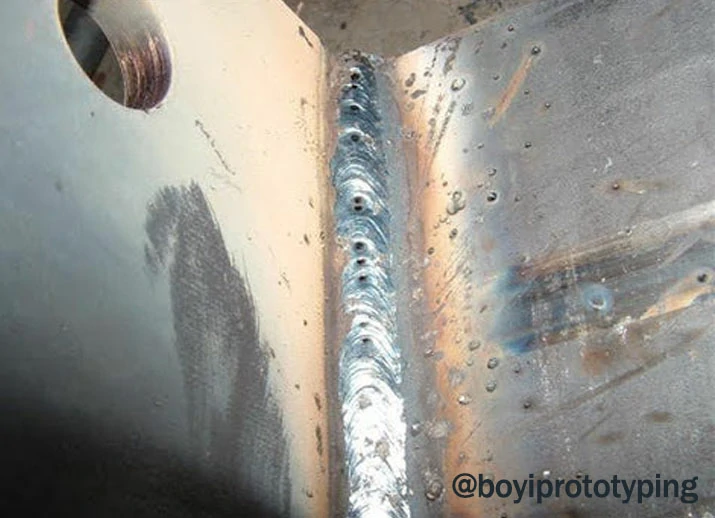
Advanced Solutions for Porosity Control
Carrying out advanced technologies and ingenious approaches plays a crucial duty in attaining remarkable control over porosity in welding processes. One sophisticated service is making use of sophisticated gas mixes. Securing gases like helium or a blend of argon and hydrogen can help in reducing porosity by supplying better arc stability and enhanced gas protection. Additionally, utilizing innovative welding techniques such as pulsed MIG welding or customized ambience welding can additionally assist reduce porosity problems.Another advanced remedy includes using advanced welding equipment. Using devices with built-in attributes like waveform control and sophisticated power resources can boost weld top quality and decrease porosity dangers. In addition, the application of automated welding systems with precise control over criteria can dramatically decrease porosity flaws.
Moreover, integrating sophisticated monitoring and inspection innovations such as real-time X-ray imaging or automated ultrasonic screening can assist in identifying porosity early in the welding process, enabling prompt corrective activities. In general, integrating these innovative solutions can greatly boost porosity control and boost the general top quality of welded you can try these out parts.
Verdict
In verdict, recognizing the science behind porosity in welding is essential for welders and fabricators to create high-grade welds - What is Porosity. Advanced solutions for porosity control can further improve the welding process and make certain a solid and dependable weld.Report this wiki page